

The most important operating variables are wheel speed and traverse rate. Wheels with 50% or lower concentration of diamond are very poor performers and should be avoided. The extended life of these diamond wheels outweighs the cost. There is no doubt that an increase of diamond up to 125% greatly improves the grinding performance. One very important consideration is the concentration of diamond in the wheel. In other words, the softer grades of carbide cause greater diamond wheel wear. The greater the cobalt content in the carbide, the greater the diamond wheel wear will be. Some are harder on diamond wheels than others. There is a definite difference in the "grindability" of various grades of carbide. By using a fine wheel and putting a good finish on the saw teeth, it is often possible to solve this saw problem.

If a saw pushes hard and tends to wobble in the cut, the problem can often be traced to rough grinding. Again you will have to be the judge of your customer's requirements. These wheels, however, grind slower and require more time to finish a saw. Generally, wheels with 150 grit, 75 concentration, and R hardness are used for regular grinding.įiner grit wheels will give better finishes on the carbide and improve the cut quality, lengthen life between sharpening, and require less power than saws with rough grinds. You must carefully select the wheels that work best for your operation. Diamonds also come in different grades and in different coarsenesses. Due to the fact that metal bonds are too hard and severe for carbide grinding, we shall limit our discussion to resin bonds.ĭiamond wheel manufacturers make resin bonds in numerous grades and hardnesses. Metal bonds work well on non-metallic materials such as glass, ceramic, stone, etc. There are two major bond types resinoid and metal. Even though coated diamonds last longer, they do create more grinding heat and do not grind as cool as plain diamonds do. It is generally accepted that copper coated diamonds are best suited for dry grinding, and nickel coated diamonds are best suited for wet grinding. Of course the metal coating of diamonds with nickel and copper has also added greatly to their life. Today these diamonds are more uniform in size and resist shock better than natural diamonds. Some 40 years ago, manufactured diamonds were introduced to industry, and since that time its use has expanded tremendously. It is up to you to figure a successful proportion of diamond and labor costs that will give you the return you are looking for. There is one fact that you must be aware of you have to use up diamonds to grind carbide. This lesson in economics is only meant to impress you with the need for a practical approach to the use of diamond wheels and the fact that labor is a far more costly part of the grinding job. Bear in mind that if you grind one saw for $10.00 in 15 minutes and use $2.00 worth of diamond, you are far better off than to grind the same saw in 30 minutes and use $1.00 worth of diamond. There can be a point of no return when too much wheel is used or too much labor. One way of arriving at diamond wheel cost is to add the cost of the wheel and the cost of the labor required to produce a certain dollar volume of work. For more articles on Grinding or Sharpening Saw Blades.
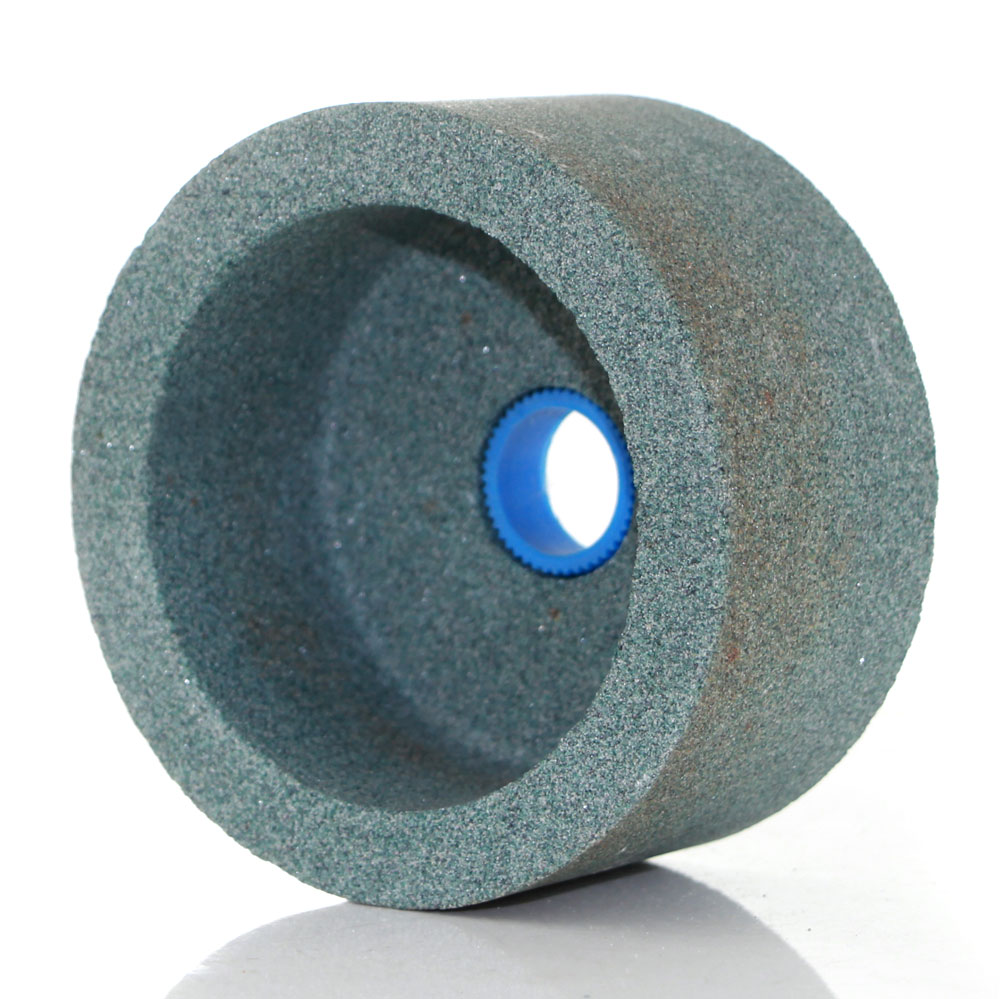
#How to grind carbide cracked
This is a very false economy and you will pay in lost time as well as in cracked and poorly ground carbide. Think this over very carefully and do not get talked into purchasing a wheel simply because it will last longer than any other. The first question you should ask yourself is: What do I expect from a diamond wheel? Your answer should be a wheel that removes carbide fast and cool.
#How to grind carbide how to
Basic Carbide Saw Tip Information and How To Order.Grinding Carbide- Health and safety risks.
